What is Six Sigma Certification? Six Things You Should Know
A business is run on the work of different cross-functional teams with the understanding that each person adds unique expertise and skill sets. Continuing to develop those skills through certifications and training, like Six Sigma, can be a fundamental part of a business's—and each employee's—success and growth.
Continual quality control and improvement are at the heart of management systems like Total Quality Management (TQM), which began as total quality control in the mid-1950s, wrote Jim Folaron in the American Society of Quality's (ASQ) "Six Sigma Forum Magazine."
It was from TQM and earlier quality initiatives that Six Sigma evolved. According to Folaron, "What is new, and what makes Six Sigma so powerful, is the combination of these elements with a rigorous, disciplined approach and well-publicized, proven business successes."
If you've spent time in a business, management or another professional or educational setting within the past two decades, you may have encountered this particular approach. But what exactly is the Six Sigma concept?
What is Six Sigma Certification?
“(Six Sigma) a data-driven, disciplined, structured problem-solving philosophy and strategy (along with an associated set of tools) used primarily to improve processes,” said Lisa Hayes, adjunct faculty at Southern New Hampshire University.
The lowercase Greek letter sigma, σ, represents the standard deviation or amount of variability. “Every process that produces something, whether you’re baking a cake or making a product in a factory, is going to have some level of variation,” Hayes said. “Six Sigma is an attempt to analyze the process, figure out where the variation, error, waste, or defect is coming from, and then eventually minimize or eliminate it.”
“A company's performance is measured by the sigma level of their business processes. Traditionally companies accepted three or four sigma performance levels as the norm,” wrote Thomas Pyzdek and Paul Keller in “The Six Sigma Handbook: A Complete Guide for Green Belts, Black Belts, and Managers at All Levels.” The higher the sigma level, the lower the error rate. And a lower error rate translates into improved efficiency and value for customers, which in turn benefits the bottom line of the business or organization.
Requirements for achieving Six Sigma certification
In order to complete your Six Sigma certification, there are a few requirements to achieve along the way. "The requirements for seeking Six Sigma include completing a course which leads to a certificate of completion," said Dr. Toni Clayton executive director of health professions and Six Sigma black belt.
Completing the 6 to 8-week course, however, does not result in your certification. "To become certified requires taking an approved Six Sigma examination where you can earn the official belt which registers an individual with their own certification numbers."
With that basic definition and requirements down, here are six other things you should know about Six Sigma.
1. The Six Sigma process features two main project methodologies.
The first is DMAIC, a multi-step problem-solving process for improving an existing business process. According to iSixSigma, which publishes regularly on process improvement methodologies, the five phases of the DMAIC process are:
- Define the project goals and deliverables.
- Measure the process to determine current performance. “At this stage, you want to determine what kind of data you will collect: quantitative or qualitative,” said Hayes.
- Analyze the data to determine the causes of variation, defects, or errors. “As part of the Six Sigma process, you can use a variety of statistical tools, from Pareto charts to affinity diagramming,” Hayes said.
- Improve the process by eliminating variation, defects or errors. “Based on the data, you decide what improvements you want to put in place,” Hayes said. “Then you come back later and collect more data to be able to say, ‘Yes, I did make a difference and I can prove statistically that I did so.’”
- Control future process performance. “You’re constantly monitoring to ensure the improvement stays in place,” said Hayes.
Per ASQ, “While DMAIC is not the only Six Sigma methodology in use, it is certainly the most widely adopted and recognized.” The other main Six Sigma methodology is DMADV, used for creating new or completely different products, services or processes. The five DMADV phases are:
- Define the project goals and deliverables (the same first step as with DMAIC).
- Measure and determine customer/client needs and specifications.
- Analyze the process options to meet customer needs.
- Design in a detailed way, the process that meets customer needs.
- Verify the design performance and ability to meet customer needs.
2. There are several levels of Six Sigma certification.
Six Sigma certification programs, each with their own requirements and criteria, are offered by professional associations, colleges and universities, and training organizations.
You can get certified at various Six Sigma levels, known as Six Sigma belts:
- Six Sigma Master Black Belt – These professionals are, according to Pyzdek and Keller, “highly proficient in using Six Sigma methodology to achieve tangible business results.” They have additional specialized skills and technical expertise beyond the Black Belt level.
- Six Sigma Black Belt – Black Belts “are the doers, the technical leaders and change agents in an organization," per ASQ. They are project leaders who also coach and mentor Green Belts.
- Six Sigma Green Belt – These individuals “serve on project teams to help collect and analyze data, develop process maps, assist the Black Belt in some levels of statistical analysis, and even develop experimental designs for a particular project,” according to ASQ.
- Six Sigma Yellow Belt – “Yellow belts have a basic understanding of the concept as well as some familiarity with the analytical and problem-solving tools,” said Hayes.
ASQ identifies additional levels, including Six Sigma White Belt (team members with an awareness of Six Sigma concepts), plus Champions and Executives (leaders who “set the direction for selecting and deploying projects”).
3. Six Sigma jobs are not only in the manufacturing industry.
Although most closely associated with manufacturing processes, Six Sigma can be applied across a range of industries.
“It doesn’t matter what type of an organization it is,” said Hayes. “It’s very commonly used in business settings for quality management, but it’s more of a cultural mindset. If you can collect data, measure and analyze it, you can really use this method for any kind of problem solving.”
According to iSixSigma and Hayes, industries using Six Sigma include:
- Energy
- Financial services
- Government
- Health care
- Higher education (per Gallup)
- Hospitality
- Insurance
- Pharmaceuticals
- Retail
- Software/IT
- Telecommunications
- Transportation and logistics
And a sampling of job titles preferring or requiring Six Sigma knowledge or certification include:
- Quality manager
- Quality assurance analyst
- Performance improvement coordinator or specialist
- Business process engineer
- Senior manager for process excellence
- Continuous improvement champion or leader
4. There's a lean approach to Six Sigma, too.
OK, so now you have a grasp of the Six Sigma methodology, but what is Lean Six Sigma? Lean Six Sigma combines lean manufacturing or production with Six Sigma’s focus on eliminating variation.
“The concept behind Lean is that customers should only pay for what’s valuable to them. Anything that doesn’t add value to the customer should be eliminated because it’s waste,” said Hayes. “Lean uses many of the same tools as Six Sigma to eliminate waste, so it goes hand in hand with classical Six Sigma, which focuses on eliminating variation in the output, which is another kind of waste."
Today, “the Lean Six Sigma methodology is practiced by tens of thousands of professionals worldwide,” according to the International Society of Six Sigma Professionals.
5. The benefits of Six Sigma impact professionals, organizations, and consumers.
Six Sigma education, training or certification “does add to your resume,” said Hayes, “especially in the manufacturing environment but also in the service industries. Six Sigma is so prevalent in industry nowadays that having a background in Six Sigma principles, processes and tools does help your career path.”
It can also result in a salary bump. ASQ's 3nnd annual Quality Progress Salary Survey found that professionals with a Six Sigma certification earned $16,000 more annually than those without one. Professionals with two Six Sigma certifications earned more than $11,000 annually than those with one certification, according to the survey of more than 6,000 respondents.
While Six Sigma training for leadership and employees is a significant investment of time and money, the result is “that you have a common language, and that language is ‘Show me the data.’ It’s not about opinion, history, or anecdote. Instead, it’s data-driven,” she said. The increased availability of data today means there are more opportunities to leverage Six Sigma across a range of industries.
"It’s absolutely worth obtaining a belt at any or all of the levels. An official certification in any of the belts represents that you learned a set of skills which can be applied to any work setting at various degrees," said Clayton
Finally, a benefit and one of the top reasons to get your Six Sigma certification is the signaling that results from the certification or training.
“Your customers know that as a Six Sigma organization, your intention is to produce defect-free products or services. For many businesses and organizations, that’s worth the investment, which is why GE and others have been so keen on the process for so long.”
6. The history of Six Sigma begins in the mid-1980s with Motorola.
“Six Sigma was introduced by Motorola in the 1980s as a response to poor quality,” Hayes said. So, Motorola’s CEO at the time “started the company on the quality path known as Six Sigma … using Six Sigma, Motorola became known as a quality leader and a profit leader,” wrote Pyzdek and Keller.
In the mid-1990s, GE's Welch implemented Six Sigma quality control “as a business-building strategy,” wrote Gregory H. Watson in “Six Sigma Forum Magazine."
According to Watson, the GE Six Sigma initiative “was the final stage in the sequence of improvement initiatives that [Welch] championed as CEO” and it helped him attain his “current icon-like position as the global spokesman for Six Sigma.”
Learn about how a Six Sigma Certificate program can help prepare you for the Black Belt Certification exam and build your career.
Sofia Tokar is a freelance copywriter and editor in higher education. Follow her on Twitter @stokar or connect on LinkedIn.
Explore more content like this article
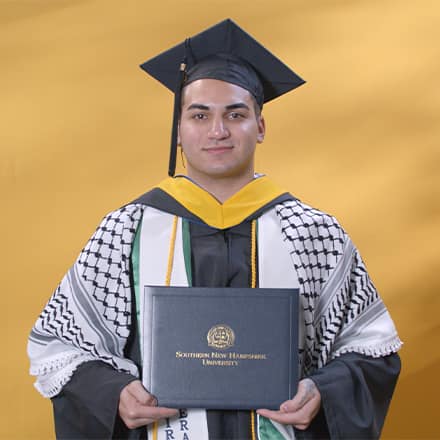
SNHU Spotlight: Jonathan Oubenslimane, BS in Business Administration Grad
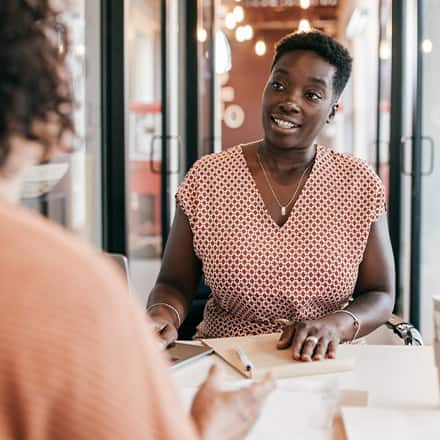
How to Become a Recruiter
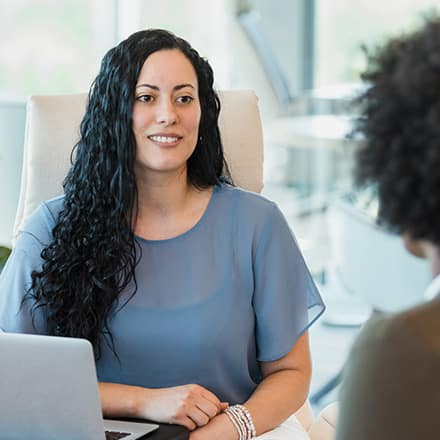
What Degree Do You Need for Human Resources?
About Southern New Hampshire University
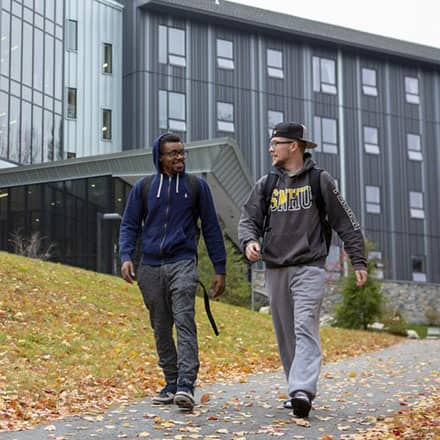
SNHU is a nonprofit, accredited university with a mission to make high-quality education more accessible and affordable for everyone.
Founded in 1932, and online since 1995, we’ve helped countless students reach their goals with flexible, career-focused programs. Our 300-acre campus in Manchester, NH is home to over 3,000 students, and we serve over 135,000 students online. Visit our about SNHU page to learn more about our mission, accreditations, leadership team, national recognitions and awards.